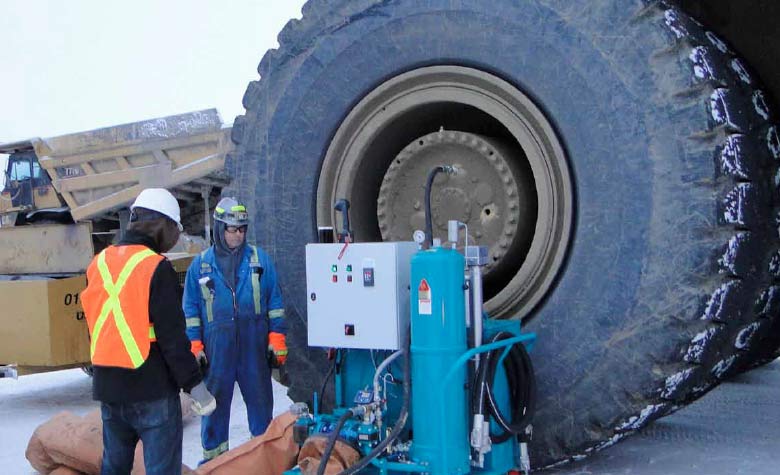
They say that in order to get a job done well you have to get your hands dirty from time to time, and a truer statement was perhaps never spoken than when it comes to the mining industry. The sheer scale of the equipment used and the nature of the environments that are being operated in make mining a highly maintenance intensive undertaking. This inevitably results in a large concentration of dirt being produced. With this dirt having the ability to contaminate virtually everything in the surrounding area, it is clear that it takes more than a bit of soap and elbow grease to remedy the problem.
A family-owned, international business established in 1953, C. C. JENSEN has been manufacturing lubrication oil filters for marine engines for 60 years. In the time since, it has refined off-line depth filtration for a wide range of applications in the wind, power, industrial and mining sectors. Today, its CJC™ Fine Filters and CJC™ Filter Inserts are available through a worldwide network of sales consultants and service professionals.
Mine and quarry customers today use CJC™ Fine Filters to maintain clean oil in drilling equipment, crushers, haul and dump trucks, excavators, conveyor belts, bulk storage tanks and other miscellaneous equipment. “To date,” explains Account Manager, Caren Caffrey, “we have been active in the mining sector in Mexico, Chile, South Africa and Australia. Meanwhile, we are strengthening our market position in the US and Canada as never before.”
What C. C. Jensen has introduced to the industry, and what has already brought it success in the aforementioned markets, is the ability to provide Clean Oil. “The filter media that we use,” Caffrey continues, “is very unique in that it possesses a large surface area in comparison to other filter media. This allows the system to capture a greater amount of dirt, particulates, water and varnish from the oil in question. Incorporating the CJC™ Fine Filters allows the customer to reduce oil consumption and equipment downtime, which naturally increases operation productivity.”
Over the last decade or so, significant changes have occurred within the mining sector as it relates to oil cleanliness. Driven by the likes of Caterpillar and other equipment manufactures that have established minimum standards of oil cleanliness for their products, large mines are now beginning to set their own minimum oil cleanliness standards across their organisations. What they often find however, is that the filtration systems they have in place do not meet the new standards.
“Those companies that have tried our products love them,” Caffrey enthuses, “mostly because they help the company meet or exceed today’s standards of oil cleanliness. Our products can filter any viscosity oil, meaning that where a lot of other systems, particularly inline filters, are limited to lower weight oils, ours can tackle those thick, heavy duty lubricants at ISO 320 or ISO 680 and above that others can’t.”
C. C. JENSEN’s products also boast significant environmental benefits, the first being the fact that their filter inserts are made from a renewable, sustainable resource. A combination of pulp fibre and cotton, this organic material can be disposed of in a green manner that avoids the use of landfill sites.
The other primary benefit from a sustainability perspective is, of course, that the company’s products’ core purpose is to create Clean Oil. “By keeping that oil clean,” Caffrey highlights, “the first thing you do is reduce the frequency at which the oil has to be replaced. This subsequently reduces your carbon footprint by scaling back your demand for these lubricants.”
As Caffrey goes on to state, the company is observing a greater degree of open mindedness from the mining sector to try new things when it comes to oil filtration, and where this is occurring, the results have been very positive. “Recently, we have been working with a company operating with the Canadian oil sands. Here we have put to use one of our more recent product launches, which is a large, Mobile Flushing Unit with an on board heated reservoir and particle counter. With this unit, we pump warm, heavy lubricant into the rear differentials of the big haul trucks during scheduled PM outages and clean the oil to recommended levels within a few hours. Cleaning the oil rather than simply replacing it has increased the lifespan of these differentials from 18,000 to 25,000 hours. Based on the size of their fleet, the company has calculated that this will help save them an average of $500,000 dollar per year.”
Other avenues that C. C. JENSEN is currently looking into include the installation of filtration systems on diesel storage tanks and the development of heavy duty filtration systems for mobile equipment. “We already have some small, heavy duty filters in service,” Caffrey says, “and larger units that are in the design stage. With their stronger mounting brackets and stabiliser packages, these systems will withstand the tough conditions encountered while installed onto mobile equipment such as drilling rigs and excavators.”
With respect to the immediate future, the next big push for the company will be in the field of explosion proof motors, which will be required for the underground coal mining sector.
“Right now,” Caffrey says, “we see great potential for mining companies in North America to take control of reliability by controlling contamination. These improvements in reliability and productivity will have a significant impact on the bottom line for mining operations. We have a wealth of knowledge, case studies and practical experience that we are eager to use to help our customers solve their oil related problems. In addition, C. C. JENSEN provides a 100 percent satisfaction guarantee on all products.”
Caffrey concludes, “I really believe that there is a Clean Oil revolution occurring. Machine reliability is no longer a desire, but a demand. Effective contamination control is a key enabler to success. I expect that CJC™ Filters will become a standard solution that all engineering companies and mines will expect to have as a filtration solution on all of their critical equipment.”
Written by Will Daynes, research by Gareth Hardy